Polymaker y XEV han reunido dos de las tendencias tecnológicas actuales más de moda: la propulsión eléctrica y la impresión 3D. Han desarrollado el LSEV, un coche eléctrico ultracompacto que se imprime en 3D en un proceso de solo tres días y que se vende al público por un precio de 10.000 dólares, que al cambio suponen unos 8.000 euros.
Ambas compañías defienden que se trata de un modelo urbano totalmente capaz en el que prima la sencillez. Apenas mide 2.489 mm de largo, 1.295 mm de ancho y 1.498 mm de alto; pesa 450 kilos y está compuesto por 57 partes impresas a partir de poliuretano termoplástico (TPU), ácido poliláctico y nailon.
Lógicamente esto no supone el vehículo entero, puesto que luego se incorporan el chasis, los asientos y todos los cristales, que se fabrican a la antigua usanza; pero aun así su proceso de producción es bastante más sencillo que el de un coche tradicional, que con características similares suele estar formado por 2.000 piezas y roza la tonelada de peso. Por compararlo con el Smart fortwo, al que recuerda en diseño y proporciones, es solo 20 centímetros más corto y 40 centímetros más estrecho, pero pesa casi la mitad (440 kilos menos).
Sobre su mecánica eléctrica se desconoce la potencia, pero sí se ha revelado que su velocidad máxima será de 69 km/h (es un vehículo eminentemente para uso en ciudad) y que su autonomía llega casi a los 150 kilómetros. En esto tampoco se diferencia mucho del Smart, que homologa 160 kilómetros de rango de uso.
Por el momento la compañía afirma que han recibido 7.000 pedidos del LSEV, la mayor parte de ellos originarios de Europa. Las entregas comenzarán en abril de 2019 y esperan haber producido 20.000 unidades para cuando acabe dicho año.
https://www.youtube.com/watch?v=M-X-rN2yXfs
GRUPO VOLKSWAGEN
Esta apuesta por el 3D no es única. Volkswagen trabaja en un proyecto para imprimir piezas de recambio para sus coches clásicos. Con los proveedores originales fuera del mercado, esta tecnología supone la solución para mantener con vida a modelos históricos de la marca. Lo explica Tobias Pape, Purchasing Manager Classic en Volkswagen Classic Parts: “Especialmente para pequeñas cantidades, la impresión en 3D abre un gran abanico de nuevas posibilidades para nosotros”.
No es la primera vez que se lleva a cabo el proceso dentro de la compañía: “La impresión en 3D en el grupo Volkswagen se ha utilizado hasta ahora solamente en las áreas de construcción de prototipos y equipamiento. Ahora queremos aplicar este conocimiento interno para la producción de piezas de recambio”.
El proyecto piloto se ha realizado con un adaptador del elevalunas (manual, por supuesto) del Volkswagen Corrado. Aunque pueda parecer insignificante, es un elemento que reunía las tres características que buscaban desde Volkswagen Classic Parts: no ser visible una vez instalado, tener una mínima relación con la seguridad y ser tan pequeño como fuera posible. Pape apunta que “reproducir este adaptador es un auténtico reto. Particularmente debido a que el fino estriado interno y externo del engranaje requiere un importante un alto nivel de precisión”.
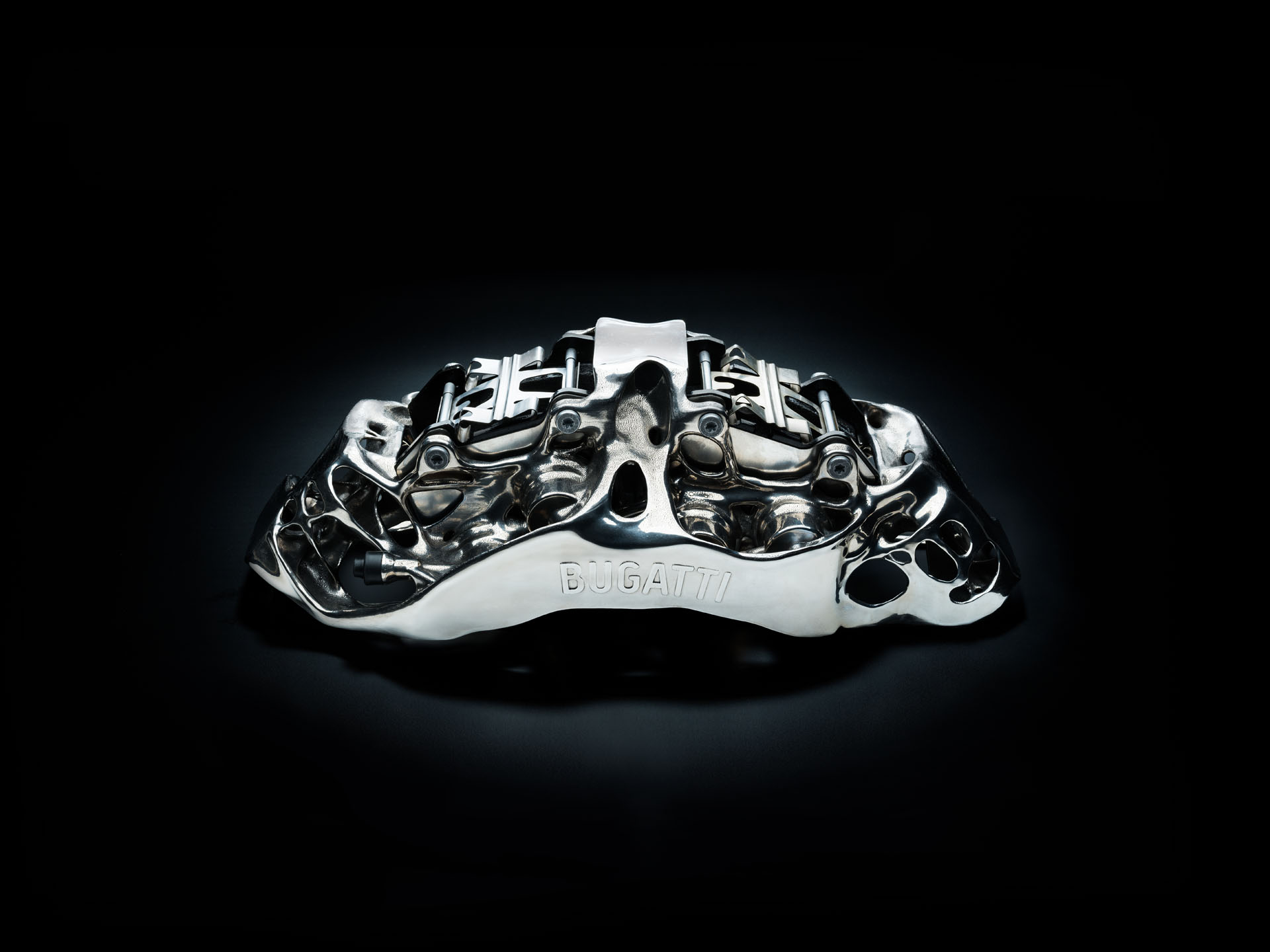
La pinza de freno del Bugatti Chiron.
PARA EL BUGATTI CHIRON
Si se trata de hablar de piezas concretas, Bugatti se lleva la palma. La marca hizo un ensayo de lo más innovador al imprimir en tres dimensiones la primera pinza de freno de titanio del mundo, empleando 2.213 capas del material.
La aleación de titanio utilizada en las pinzas 3D del Bugatti Chiron ofrece un rendimiento mucho mayor, ya que resiste una fuerza de hasta 125 kilos por milímetro cuadrado antes de romperse. Además, es mucho más ligera: pesa solo 2,9 kilos por los 4,9 habituales, hasta un 40% menos. Y todo ello sin reducir sus dimensiones, ya que mide 410 mm de largo, 210 mm de ancho y 136 mm de alto.
Un punto importante es la capacidad de tratar el titanio mediante impresión 3D, algo que hasta hace no mucho era inconcebible. Para conseguirlo se utilizó la impresora del Laser Zentrum Nord (Hamburgo, Alemania), la más grande del mundo cuando empezó el proceso. Sus cuatro láseres de 400 vatios derriten el polvo de titanio para darle la forma adecuada en una operación que dura 45 horas, y para la que se emplean 2.213 capas del material.
Sigue toda la información de EL MOTOR desde Facebook, X o Instagram