La llegada de los coches eléctricos ha traído cambios también en la manera de fabricarlos. Su estructura, diferente a la de los automóviles de combustión, permite emplear nuevos sistemas de producción más rápidos que los tradicionales, sistemas que Xiaomi está utilizando para fabricar una unidad tras otra de su primer coche, el SU7.
La planta en la que se monta la berlina eléctrica obtiene de su línea de fabricación una unidad cada 76 segundos, algo posible gracias al empleo de dos técnicas distintas: la fundición y el estampado.
La primera fue puesta de moda por Tesla y se trata de un proceso por el que se reemplazan varios componentes individuales por una pieza de mayor tamaño que los integra mediante la fundición. Esto tiene varias ventajas, y una de ellas es que la pieza resultante presenta una mayor rigidez que la suma de las partes por separado, por lo que se simplifica el proceso de manufactura y se aligera el peso del coche.
Más información
Xiaomi la ha combinado con el proceso de estampado de piezas para conseguir un sistema eficiente que reduce el uso de componentes y el tiempo de fabricación.
Integrado en el interior de su fábrica, el sistema responde al nombre de 9100T y ocupa lo mismo que dos campos de baloncesto. Cuenta con un alto grado de automatización, por lo que se encarga de dar forma a la base de cada Xiaomi SU7 por su cuenta.
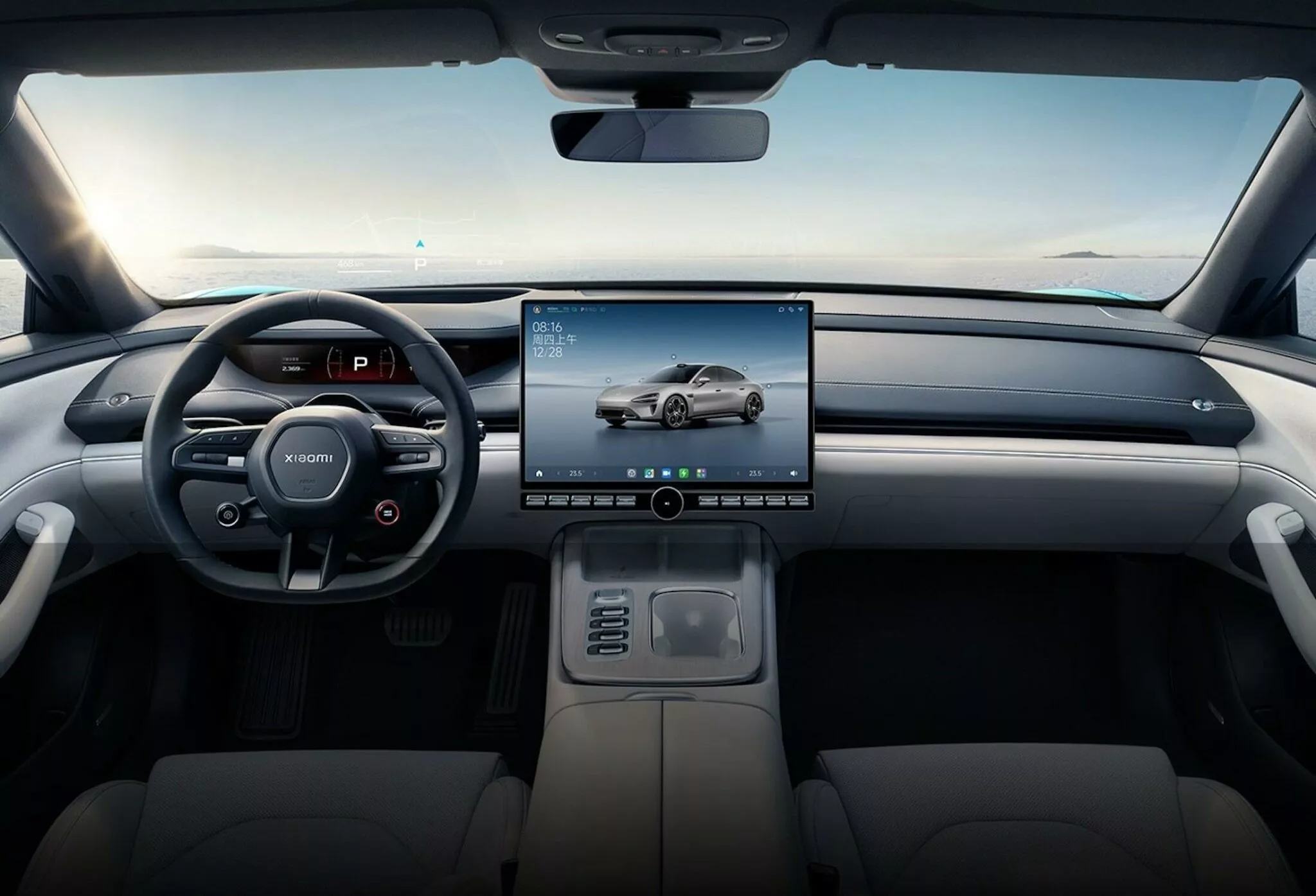
Las ventajas de este proceso de manufactura
El uso de estas técnicas hace que la plataforma de la berlina esté formada por solo una gran pieza, en lugar de las 72 que la habrían conformado si se utilizaran otros métodos. ¿Qué ventajas tiene esto?
Se realizan 840 puntos de soldado menos, lo que agiliza la producción un 45%, creando la base en solo 100 segundos. Además, es un 17% más ligera de lo que habría sido empleando otras técnicas. También reduce en dos decibelios el ruido que llega al habitáculo proveniente de la carretera y su ciclo de vida cubre dos millones de kilómetros, 10 veces más de lo habitual.
Además, el fabricante ha trabajado para solventar uno de los mayores problemas de este sistema. Al tratarse de una única pieza de gran tamaño, el principal inconveniente es que, ante un choque, el coste de reemplazo es mucho mayor que si se tratase de elementos individuales.
Para evitarlo, el SU7 tiene un sistema antichoque de tres fases, por el que, en el caso de impactos bajos y medios, solo hay que reemplazar la zona de deformación y la sección anticolisión.
Sigue toda la información de EL MOTOR desde Facebook, X o Instagram