Los conocidos popularmente como desguaces se llaman en realidad en España Centros Autorizados de Tratamiento (CAT). Y existen 1.300 repartidos por el territorio nacional, que procesan anualmente unos 700.000 vehículos para su reciclaje.
Más información
Desde enero de 2015, la legislación europea obliga a reciclar el 95% de la masa total de cada vehículo fuera de uso. Y es una normativa ambiciosa, porque un coche moderno reúne en torno a 60.000 partes (unas 4.000 piezas), que a su vez pueden ser de hasta 40 materiales diferentes, entre ellos el metal, el plástico, los tejidos, el caucho, el vidrio y los polímeros.
Los materiales extraídos pueden reutilizarse en la industria del automóvil, revenderse como componentes de segunda mano o acabar, entre otras transformaciones, convertidos en tejidos, electrodomésticos, recipientes, aislantes y hasta suelo blando de parques infantiles.
Fase 1: descontaminación
Cuando un vehículo llega a un desguace, lo primero que se realizan son las tareas de descontaminación. Pero es solo el comienzo de un proceso complejo y a menudo desconocido. Rafael Pardo, director de la Asociación Española de Desguace y Reciclaje del Automóvil (Aedra), lo resume así: “Tras la recepción del vehículo, hay un trabajo administrativo para controlar su estado legal y procedencia. Una vez cumplimentado, se pasa a realizar la descontaminación. Y tras esta llega el despiece de los componentes, que se derivan después a otras empresas que se dedican a recuperar los diversos materiales (que los conforman) para completar el reciclado”.
El objetivo del descontaminado es extraer todas las sustancias que puedan resultar dañinas para el medio ambiente, como los gases del circuito del aire acondicionado (afectan a la capa de ozono al liberarse en la atmósfera), el combustible, los aceites lubricantes, el líquido hidráulico y la batería, que suele contener metales pesados y ácidos corrosivos. Y aunque algunos se pueden reutilizar, la mayoría se destruyen o neutralizan mediante procedimientos seguros certificados.
Fase 2: el despiece
Una vez descontaminado, los operarios del CAT proceden al desmontaje del coche en sí, extrayendo el motor y la caja de cambios, las ruedas, el capó, los faros y todo lo que, por su correcto estado, se pueda reutilizar en el mercado de segunda mano. Lo que no sea aprovechable, se queda ahí.
A las partes extraíbles de la carrocería (el citado capó, puertas, retrovisores, aletas…) se les realiza una inspección visual, aunque al motor, por ejemplo, y debido a su mayor complejidad, se le suman otros protocolos como el test de compresión, que sirve para comprobar su estanqueidad y buen funcionamiento general.
Los componentes aprobados son catalogados y almacenados para su reventa posterior. Y todo lo demás pasa a la siguiente fase, el achatarramiento, para el que se utilizan dos máquinas especializadas.
Fase 3: fragmentación y prensado
Tras despojar al modelo de lo que se puede aprovechar, el vehículo se parece ya más a un esqueleto de metal. Y su destino final se acerca. La estructura básica de la carrocería, y las partes metálicas no extraídas (una suspensión, por ejemplo), se envían a la prensadora, la primera de las grandes máquinas que intervienen en el proceso de reciclado de un automóvil.
Se trata de una prensa capaz de convertir un coche, o lo que queda de él, en un cubo de metal de aproximadamente un metro cúbico. Y estos cubos, que recuerdan a las balas de paja de los campos, se envían a las fundiciones de la industria metalúrgica.
El resto de partes que se despiezaron del coche pasan a la fragmentadora, la segunda gran máquina del reciclaje. Un potente dispositivo que tritura y separa en bruto los diferentes materiales para su clasificación. Dentro de este artilugio, las composiciones metálicas son atraídas por imanes, que se separan así del resto de elementos no férricos, como el aluminio y el cobre. Este último suele concentrarse en los cables, y no es poco: el cableado de un coche moderno suma varios cientos de metros de largo y ronda los 10 kilos.
Mientras, los demás componentes viajan hasta las plantas de posfragmentación, unos gestores especializados donde se hila más fino (también por el menor tamaño de lo que va quedando) en la separación de materiales mediante aire a presión, centrifugadoras, electrificación y otras técnicas de cribado para disgregar los diferentes materiales, como los metales preciosos (platino) que contienen los catalizadores.
Fase 4: la reutilización
El elemento más sencillo de reciclar y aprovechar es el acero de la estructura del coche. Es de muy buena calidad y pasa directamente a alimentar las fundiciones (los cubos de metal antes mencionados), de donde saldrá listo para utilizarse de nuevo en la industria, ya sea en forma de chapa para construir nuevos vehículos o de vigas para el sector de la construcción.
Los neumáticos, por su parte, ofrecen varias opciones. Si su estado lo permite, se recauchutan y vuelven a utilizarse. Si están dañados, en cambio, se trituran para convertirse en un granulado con múltiples aplicaciones: desde servir de combustible para plantas industriales, como cementeras o siderurgias, hasta la fabricación de césped artificial, de muebles, calzado e incluso de pavimento de carreteras, porque mejora la calidad del recubrimiento al mezclarse con el asfalto. Asimismo, y en una de las mutaciones más sorprendentes, este granulado puede terminar también convertido en un suelo de seguridad para parques infantiles, con efecto amortiguador.
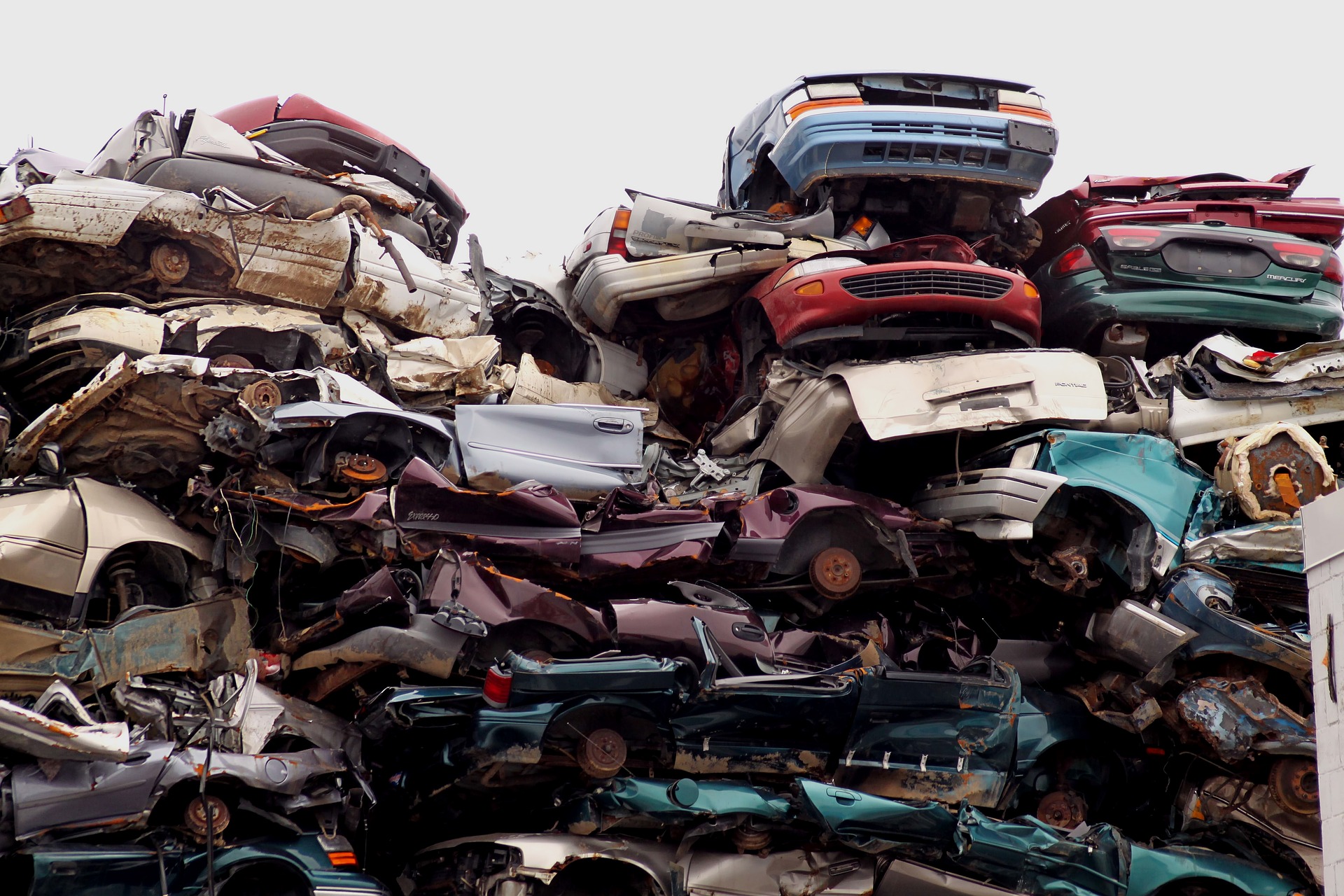
Los plásticos y elementos textiles, por su parte, sirven como base para la fabricación de aislantes, utilizados en edificios, o de vuelta en la industria automovilística, como paneles de recubrimiento interior y guarnecidos. Y el vidrio de las lunas y ventanillas se recicla para producir botellas y recipientes alimentarios.
Pero la rueda también funciona a la inversa y hay recientes ejemplos de cómo la industria automovilística empieza a recuperar materiales reciclados provenientes de otras fuentes. Audi, por ejemplo, aprovecha el material de las botellas de plástico, denominado tereftalato de polietileno (PET), para fabricar un tejido que sirve como tapicería de los asientos y de moqueta para el suelo. Con 45 botellas de 1,5 litros se puede recubrir un asiento, y en esta línea el fabricante alemán declara que su actual A3 se compone en un 83% de componentes reciclados.
Renault y Fiat aplican soluciones similares en sus últimos modelos, y Ford también, porque reutiliza 470 botellas de plástico para fabricar alfombrillas, reciclando anualmente un total de 1.200 millones de envases de este tipo. Por otro lado, esta misma marca ha firmado un acuerdo con McDonald’s para recuperar los residuos de café generados en su cadena de restaurantes y, tras mezclarlos con plástico, fabricar piezas como carcasas de faro, que resultan un 20% más ligeras y generan un menor impacto ecológico.
¿Y qué pasa con el reciclaje de los coches eléctricos?
La transición energética del automóvil hacia la electricidad plantea interrogantes en cuanto a su reciclaje. En la actualidad, el reciclado de las baterías convencionales que llevan los automóviles de motor térmico, consideradas un desecho peligroso, está resuelto por los talleres y en los propios CAT. Transportadas en contenedores especiales, son trituradas, recuperándose el plomo, que es su componente principal, para fabricar nuevos acumuladores, mientras que el electrolito (ácido sulfúrico) es neutralizado o reutilizado como decapante industrial.
Pero las baterías de los nuevos coches eléctricos (microhíbridos, híbridos, híbridos enchufables y eléctricos puros) son diferentes y, aparte de tener un tamaño y peso radicalmente superiores, contienen otros metales como el litio o el cadmio que deberán ser reaprovechados.
Por su reciente implantación y por su menor desgaste mecánico, los eléctricos todavía están lejos del final de su vida útil y de su futura llegada a los centros autorizados de tratamiento. Para Javier Arboleda, director técnico de Hyundai España, “la vida media de las baterías variará mucho dependiendo de su calidad, pero sobre todo de cómo se utilice el coche y de las recargas”.
Varias marcas fijan en el 75% o 70% la frontera mínima de rendimiento para que una batería pueda seguir utilizándose en un vehículo. Pero “con ciertos cuidados podría durar 10 o 15 años”, abunda Arboleda. “Lo ideal es cargarlas lentamente y mantenerlas siempre entre el 20% y el 80%”. Hay que evitar llegar a los extremos y, sobre todo, no agotarlas por completo”.
Pero cuando llegue el momento, ya hay alternativas previstas. Esas baterías que han perdido rendimiento y no sirven para coches pueden tener todavía una segunda vida como acumuladores en industrias, parques eólicos e incluso hogares. Y como señala el director técnico de Hyundai, “también se podrán reacondicionar, cambiando los módulos dañados, y seguir utilizándose en automóviles, como se hace ahora al reparar un motor de combustión”.
Sigue toda la información de EL MOTOR desde Facebook, X o Instagram