Todo comenzó en 1948, cuando se reformaron unos viejos talleres pertenecientes a la familia de industriales D’Ieteren en la localidad de Forest, próxima a Bruselas (Bélgica).
La finalidad de las nuevas construcciones no era otra que la fabricación de automóviles Studebaker, una prestigiosa marca estadounidense que por aquella época era una de las grandes referencias por su elevada calidad.
Más información
Impulsada por el éxito comercial y la expansión del automóvil en Europa, la actividad de este histórico centro industrial se diversificó en 1954 mediante un acuerdo con Volkswagen para producir el popular Escarabajo. La flexibilidad de la planta belga no se paró ahí, ya que en años posteriores también fabricó vehículos de las marcas Packard, Ghia e incluso produjo para el mercado local el mítico Porsche 356.
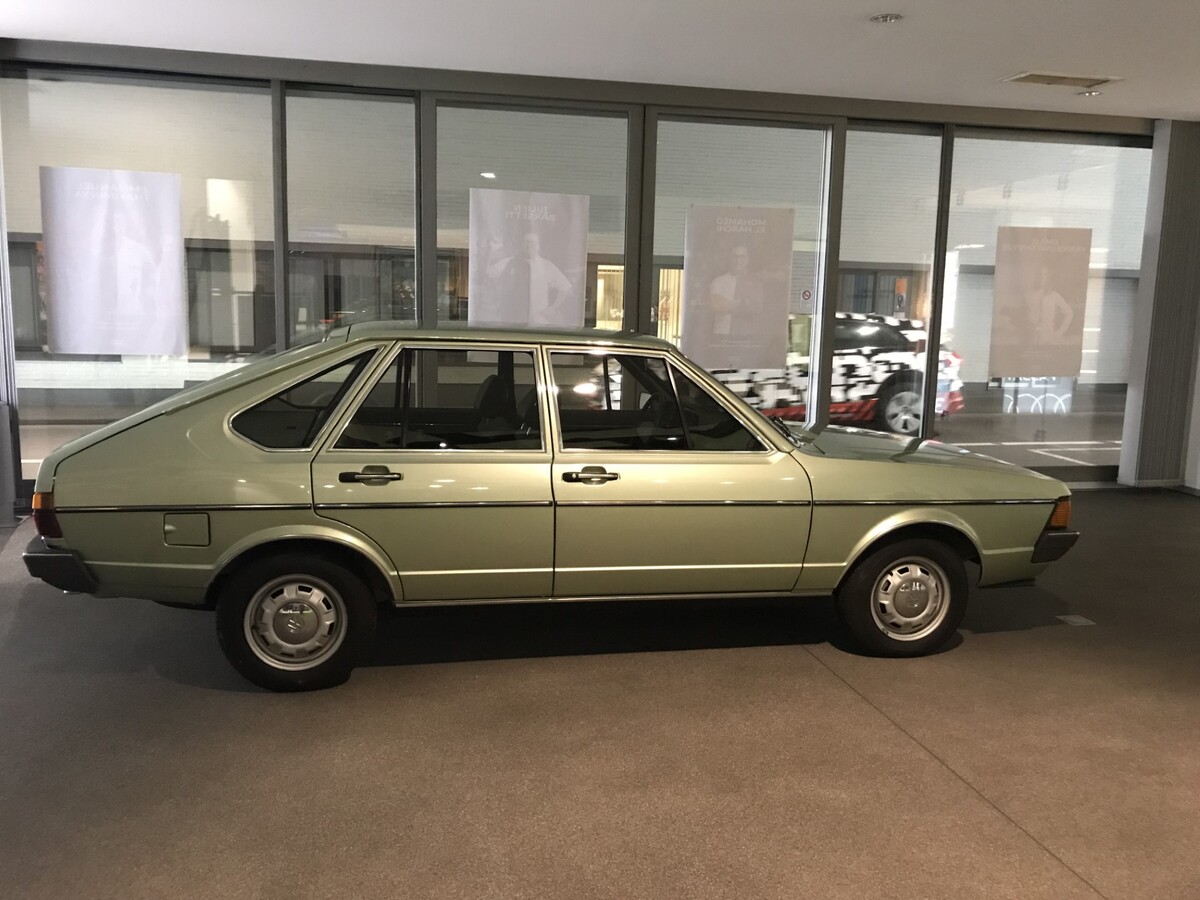
De fabricar el Audi más pequeño al más grande
Sin embargo, el desarrollo definitivo del centro se produjo cuando en 1970 la propia Volkswagen adquirió la fábrica . Tras modernizarla, adaptó sus cadenas de montaje para iniciar la producción de sucesivos modelos pertenecientes a las diversas marcas del grupo alemán, como fueron las primeras generaciones de Volkswagen Passat y Golf, o de los Seat Toledo y León.
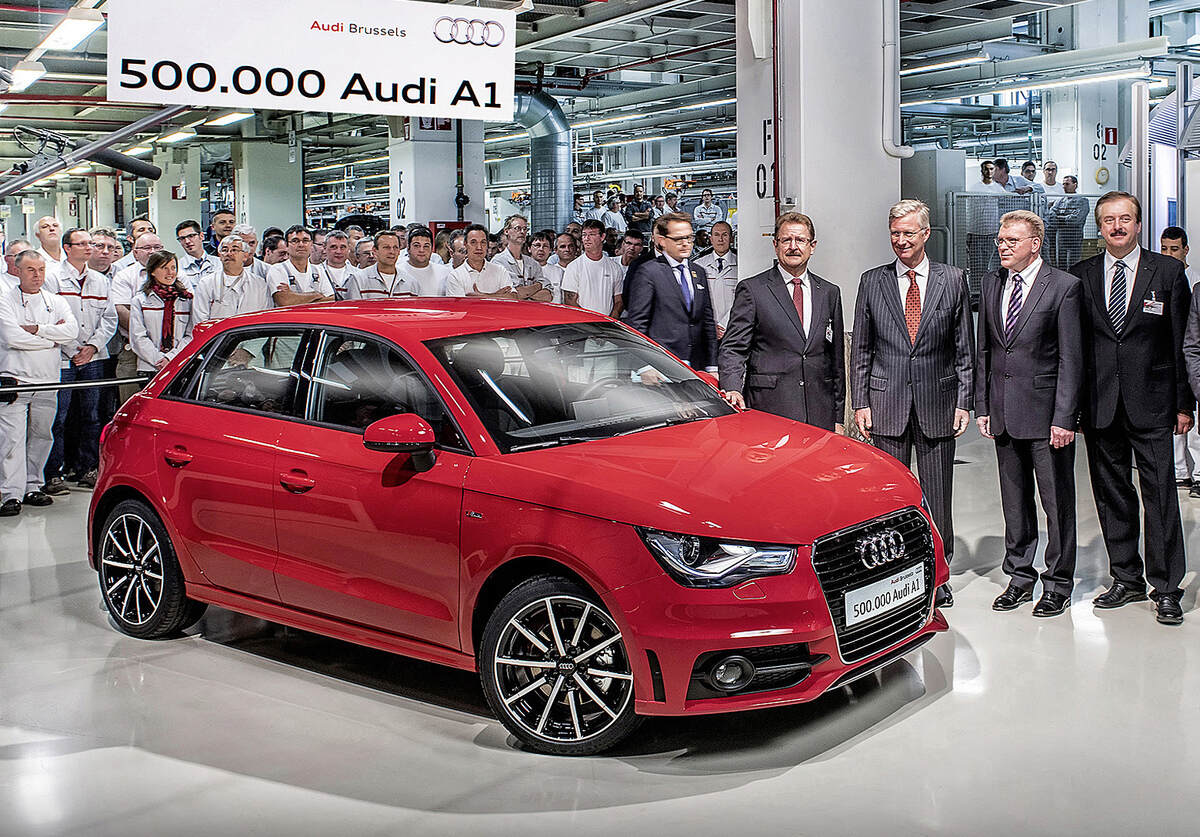
Con el nuevo siglo, la planta de Bruselas comenzó a fabricar nuevos modelos (Lupo, A3 y Polo) hasta que, ya bajo los auspicios de Audi, en 2010 llegaría su encargo más importante hasta entonces, la producción en exclusiva del utilitario prémium A1.
El paso siguiente para las instalaciones sería aún más drástico, ya que la fábrica pasó en 2018 a producir solamente vehículos 100% eléctricos, estrenándose con el e-tron, al que, dos años más tarde, se sumaría la variante cupé e-tron Sportback.
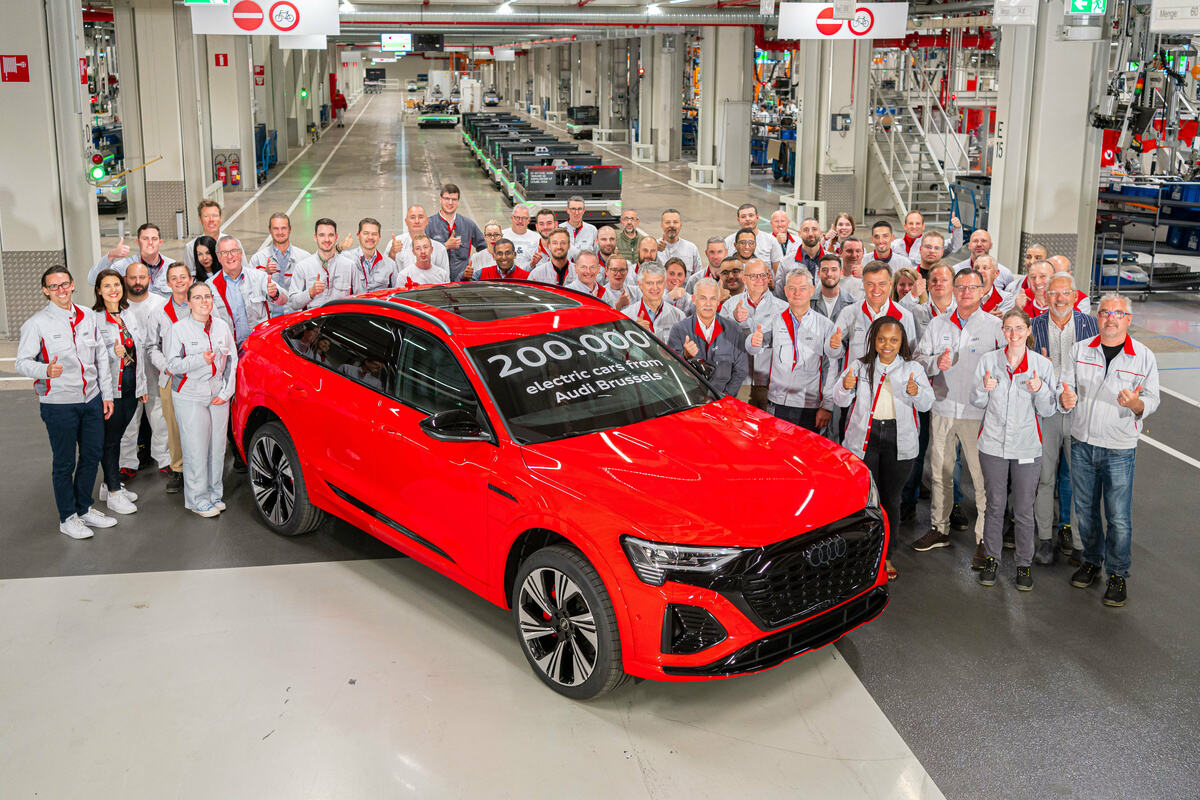
Primera fábrica sin emisiones
De producir en los últimos años el A1, el modelo más pequeño de la gama, en la actualidad Audi Bruselas ha pasado a fabricar el más grande, el eléctrico Q8 e-tron. Y, a finales de año, la marca alemana también ha confirmado que la planta belga será la encargada de suministrar también el SUV familiar a batería Q4 e-tron.
Con 2.916 empleados y ocupando una superficie de 563.321 metros cuadrados, la fábrica Audi de Bruselas es la más pequeña de la marca, pero aun así no solo se destaca por su especialización en la nueva tecnología 100% eléctrica. También lo hace por ser la primera dentro del grupo Volkswagen en conseguir las cero emisiones, adelantando incluso a la principal factoría de la firma en Ingolstadt (Alemania), que conseguirá la neutralidad de carbono en 2024.
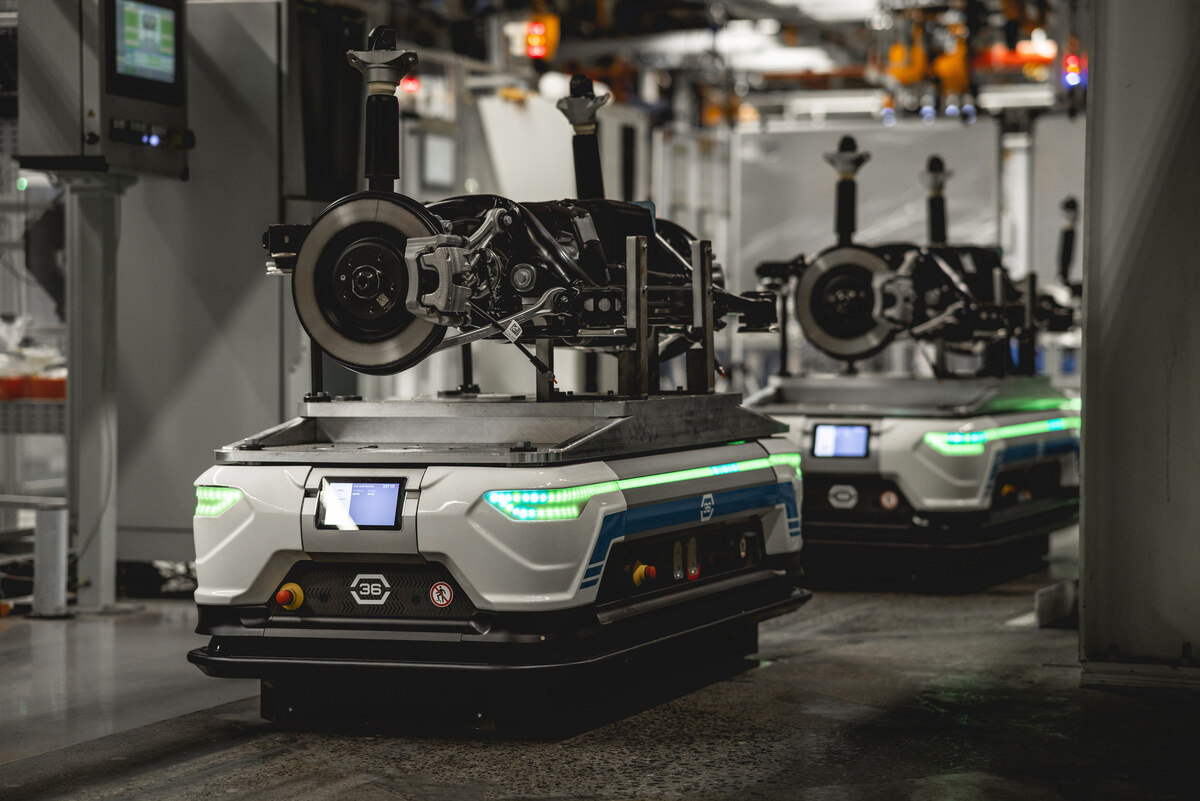
Y además de no emitir CO2 a la atmósfera, la planta de Bruselas utiliza solamente energía verde, ya sea comprada a los proveedores o la producida en las propias instalaciones, que disponen en sus tejados de una superficie de 107.000 metros cuadrados de paneles fotovoltaicos, el equivalente a 16 campos de fútbol.
La compleja producción de baterías
Por otro lado, la logística también se ha optimizado y ahora es más sostenible, porque los componentes de las baterías, que anteriormente llegaban transportados desde su origen por carretera, ahora llegan por tren. Una estrategia que apoyada por la electricidad de origen renovable ha evitado en el trayecto la emisión de 3.800 toneladas de CO2.
Hasta ahora, la planta de Bruselas ha producido ocho millones de vehículos y la transición a los modelos 100% eléctricos le han obligado a adaptarse a las últimas tecnologías.
La compleja fabricación de las baterías, de 95 y 115 kWh, a partir de los componentes suministrados por un proveedor externo, requiere cinco líneas de montaje, a través de las cuales se combina el trabajo manual de los operarios con la intervención de sofisticados robots que garantizan la seguridad y la extrema precisión que requieren algunas fases de este proceso tan complejo.
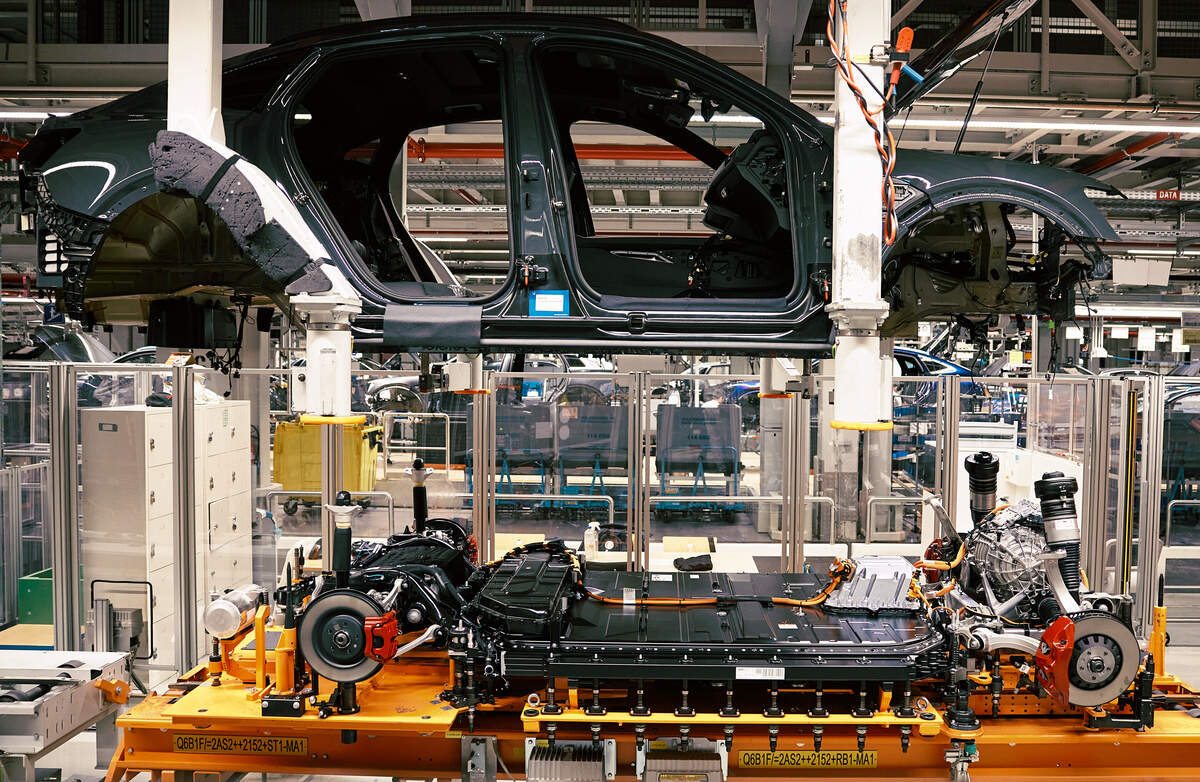
Una vez completado el proceso de fabricación, el módulo de la batería se monta en la base de la plataforma eléctrica junto a los motores, suspensiones, frenos y el resto de los componentes mecánicos que equipa el imponente SUV con hasta 408 CV de potencia.
Por otro lado, las carrocerías del Q8 e-tron son ensambladas con piezas prensadas en la planta Audi de Neckarsulm (Alemania). Un proceso que requiere una técnica muy sofisticada ya que combina el acero y el aluminio con el objetivo de aligerar al máximo el conjunto sin perder su rigidez. Y al cabo de aproximadamente unas seis horas de montaje, un nuevo Q8 e-tron ya está listo para las pruebas y verificaciones finales antes de su comercialización.
Eliminación del plástico y estudio de las abejas
Sin embargo, las innovaciones de la veterana factoría de Audi no se limitan al mero proceso industrial. Mejorar la ecología de su entorno es otro de sus objetivos, desde la eliminación de desechos (sustituyendo los envases de plástico por otros de cartón) hasta el aprovechamiento del agua, que se ha reducido a la mitad en los últimos ocho años a base de reciclarla y almacenando la de lluvia.
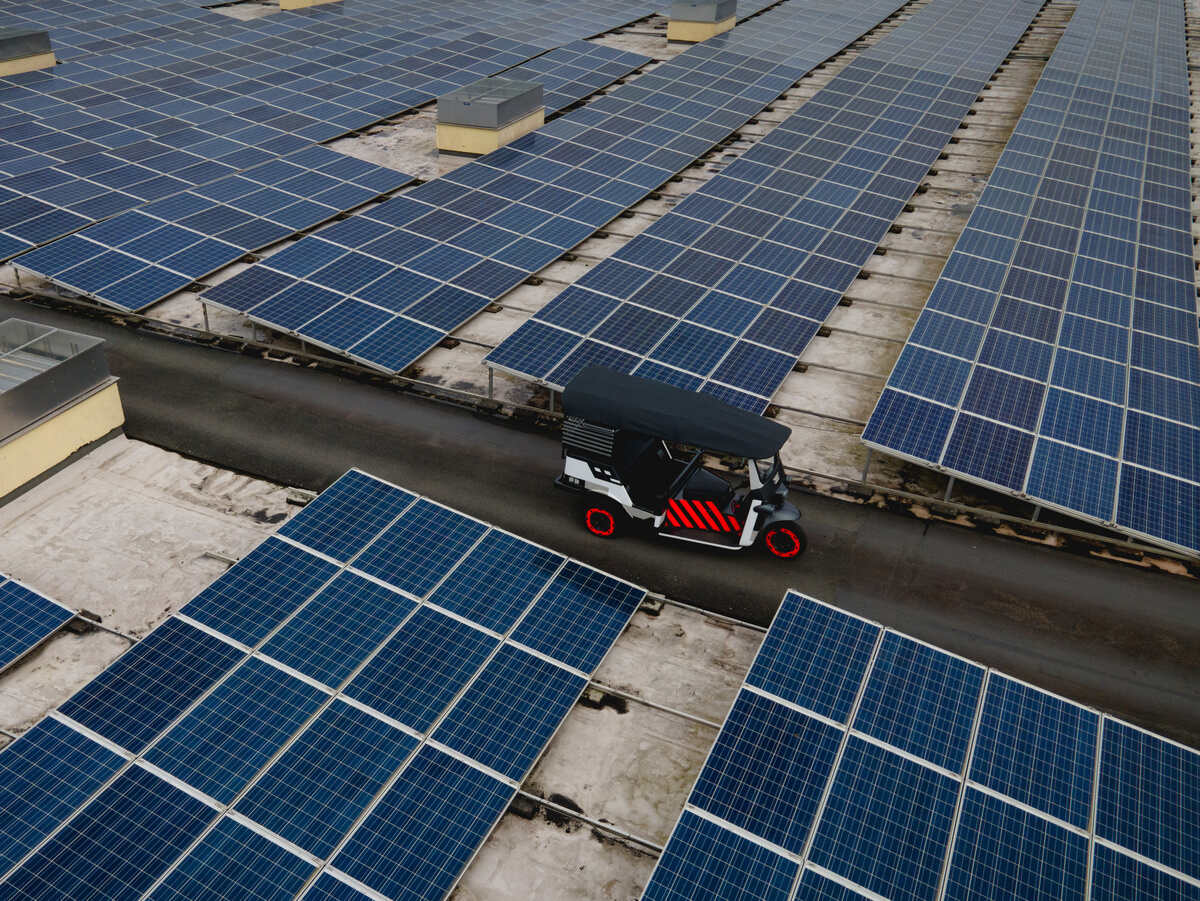
Otras acciones se han llevado a cabo en el perímetro de la propia fábrica, donde se ha mejorado el medio ambiente redistribuyendo la flora para favorecer el desarrollo de las abejas que allí habitan. Asimismo, Audi ha realizado un inventario de la biodiversidad, que ha incluido desde zorros hasta lagartos, con el objetivo de mejorar su hábitat, a la vez que se ha emprendido una acción contra las plantas invasivas que amenazan el ecosistema interior.
De hecho, la vocación ecológica y social de la marca ha llegado a lugares tan lejanos como India, donde la Audi Environment Foundation (AEF) se ha asociado con la empresa de reciclado local Nunam para darles una segunda vida a las baterías de litio, reutilizándolas después de su ciclo de vida útil en los automóviles.
Una solución de economía circular que ha sido posible gracias al sistema BattMAN ReLife, un software que diagnostica en pocos minutos el estado interno de la batería sin necesidad de desmontarla para poder determinar cuándo debe pasar a ser reciclada para otros usos menos exigentes.
Rickshaw electrificado
Entre las diversas actividades de la AEF, en India destaca especialmente un proyecto desarrollado por los alumnos becarios de la fábrica. Partiendo de un triciclo rickshaw de 1979, vehículos muy populares en los países asiáticos, los jóvenes estudiantes de ingeniería han electrificado su mecánica original, dotándole de baterías recicladas del Audi e-tron.
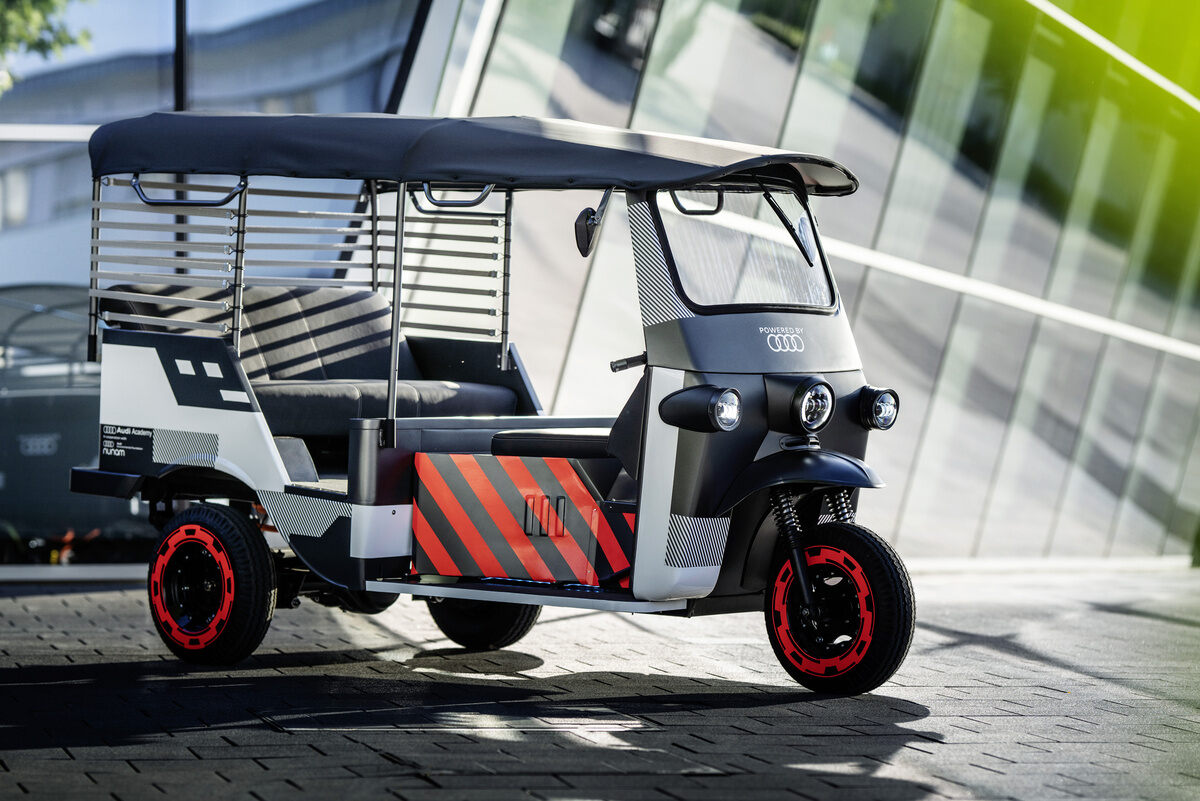
Estos vehículos, asequibles, sencillos de conducir y sin emisiones, se cargarán enchufados a pequeñas estaciones fotovoltaicas de fácil instalación. Y gestionados por Nunam, estarán inicialmente dedicados a promover iniciativas de mujeres emprendedoras indias, ayudándolas en sus desplazamientos para distribuir y vender sus productos, agrícolas o manufacturados, sin tener que depender para ello de los transportistas.
Sigue toda la información de EL MOTOR desde Facebook, X o Instagram